Collection mode heat pipe and zipper fins at present there are mainly two kinds, respectively is welding (Solder) and wear a Fin (Fin Penetration), welding process of the interface zipper resistance is low, but the cost is higher, such as aluminum fins and copper heat pipe welding, basic need to electroplating processing of heat pipe, can with aluminum fins welded together, and welding is high also to craft requirement, welding uneven or internal bubble, heat transfer efficiency will be significantly impaired.
Fin piercing is to let heat pipe directly through the Fin by mechanical means. This process is simple, but the technical requirements are no lower than that of welding, because it requires the heat Fin to have close contact with the heat pipe. If Fin piercing fails, not only the zipper efficiency will be greatly reduced, but the zipper Fin may even fall off directly.At the same time, in order to ensure that Fin array does not deform, Fin piercing process is often used in conjunction with Fin buckle technology, that is, the edge of the Fin is bent and adjacent fins are combined in the form of buckle to ensure that the zipper Fin spacing does not change.
In terms of cost, the cost of Fin piercing process is slightly lower than that of welding process, and the theoretical zipper resistance of contact surface is slightly higher than that of welding.To identify which kind of process is adopted for the heat sink, we can see by observing the zipper Fin that the welding process will leave welding holes at the contact position between the zipper Fin and the heat pipe, and the Fin piercing process is that the Fin directly wraps the heat pipe.
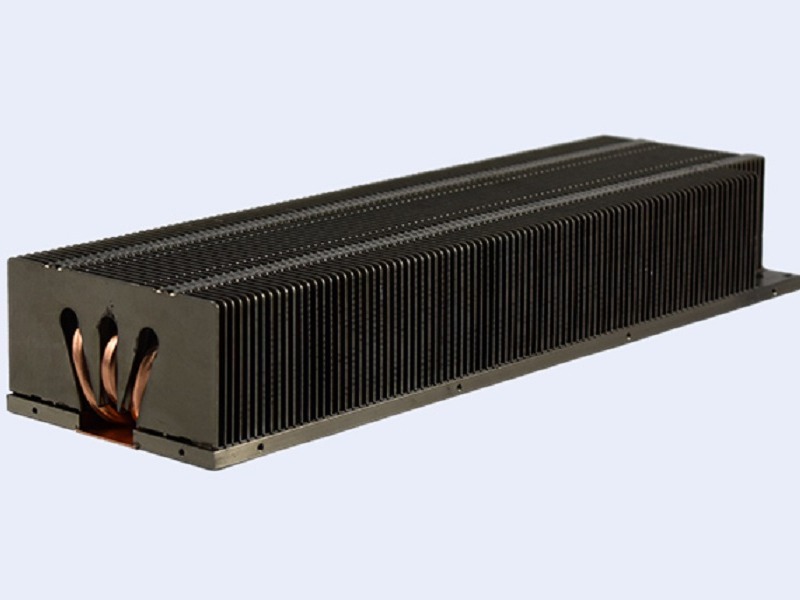
It is important to note that the excellent wear Fin process compared with welding process does not have a significant performance difference, this and the area of the cooling fins, thickness and spacing of conclusion, the key still should see the manufacturer’s technology level, but because the welding process has advantage on the durability and stability, so now most high-end heat sink use welding technology, and pay attention to the mainstream of price level product is basic in Fin process.
Conclusion: a good heat sink is not a little protruding, but every point can cooperate with each other
Heat pipe and zipper fins, base, this is the current mainstream type air cooled heat sink mainly made up of three parts, each part of the heat pipe heat sink cooling effectiveness will have an important influence, and three parts are interrelated, part simply increase would not necessarily bring heat sink efficiency of qualitative leap, but is there any part of not ready, for the performance of heat sink is a heavy blow.
Because this is an outstanding wind cool heat sink, often be not to say to have what to outstanding performance in onefold respect, depend on each respect to have better balance however, especially now the light quantification of wind cool heat sink, individuation has incline to mainstream, of this kind of balance maintain can highlight the strength of heat sink manufacturer more.
评论
发表评论